Introduction
Due to their toughness, adhesion, heat resistance and chemical resistance, epoxy resins are used in a wide variety of industrial applications including composite processes such as casting, laminating, bonding, molding and infusion. In this study we present the results of the environmental impacts associated with the production of a Liquid Epoxy Resin (LER) mix of Bisphenol and Epichlorohydrin which is used for infusion or laminating components in sports such as surfing and skiing.
The goal is to compare the different Chemicals processing routes:
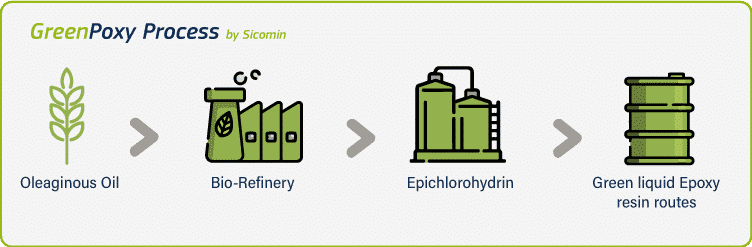
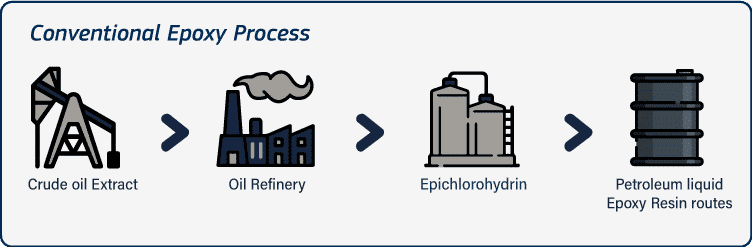
Methodology
To improve the environmental communication around bio-based products, Life Cycle Assessment is a strong tool for quantifying the environmental impact associated with the product life cycle. The study is principally performed to obtain data of environmental impacts defined into Product Classification Group (PCR): UN CPC 341 – Basic Organic Chemicals. Moreover, a link to the environmental situation around LER – production plant, different significative environmental scopes and indicators were defined: carbon footprint knowledge, human toxicity and water and air pollution indicators. (Tab 1: Environmental Impacts – CML methods):
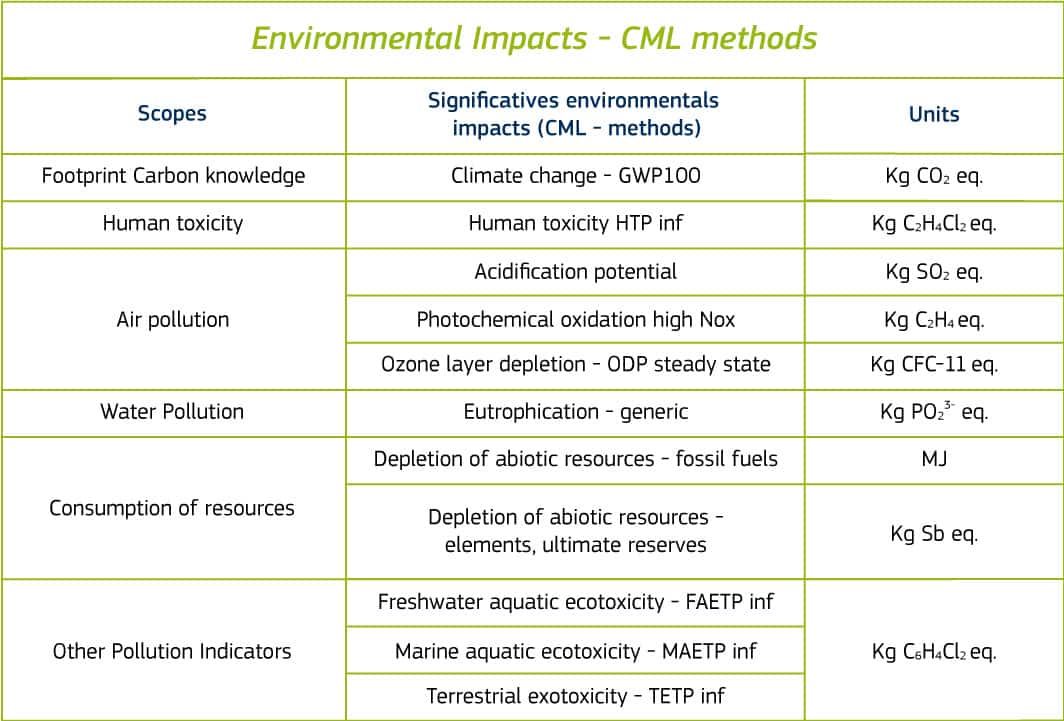
The Functional Unit for this LCA study is an average production of 1000 units of final products (skis or surfboards). With regards to the mechanical properties (Tab 2: Main mechanicals parameters compared), the Functional Unit can be simplified to 1000 kg of liquid epoxy resin (LER) produced both based on propylene (SR 1280) and based on glycerin (SR GreenPoxy).
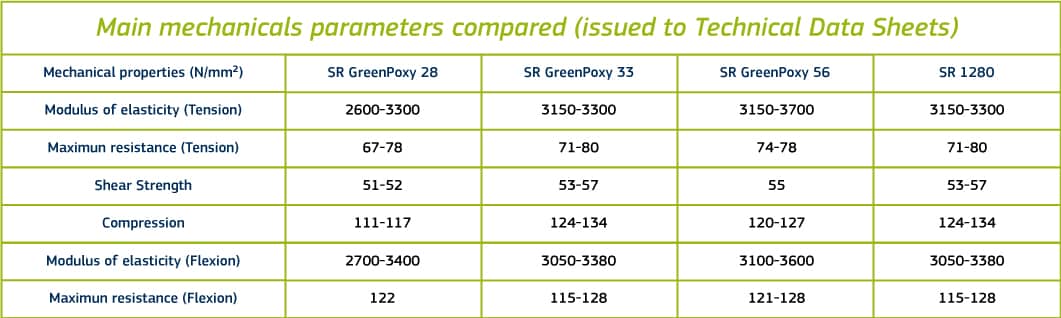
The upstream processes include the following inflow of raw materials and energy wares needed for the production of the product: extraction of petroleum resources, agricultures phases, transport of resources to refinement, refinement of resources, the production processes of energy wares used in the extraction, oil refinement and manufacturing, production of other products used such as detergents, for cleaning, fertilizer and pesticides used, etc.
The manufacturing processes include: production of epichlorohydrin from glycerin or propylene, production of the liquid epoxy resin, treatment of organic liquid and gaseous waste streams of epichlorohydrin, treatment of waste water of epichlorohydrin (lime milk and ammoniac process), industrial biological wastewater treatment of wastewater results from production in chemical plants, the production processes of energy wares used to mix and production.
The downstream processes include external transportation to the manufacturing process, treatment of wastewater in communal wastewater treatment plant, transport and disposal of commercial packaging and the final products being transported to different warehouses around the world.
Main results
The followings results (Tab 3: Main environmental impacts) were obtained with OpenLCA 1.5 software, eco-invent 3.2 database, CML calculate-methods. No normalization reference impact category results were used.
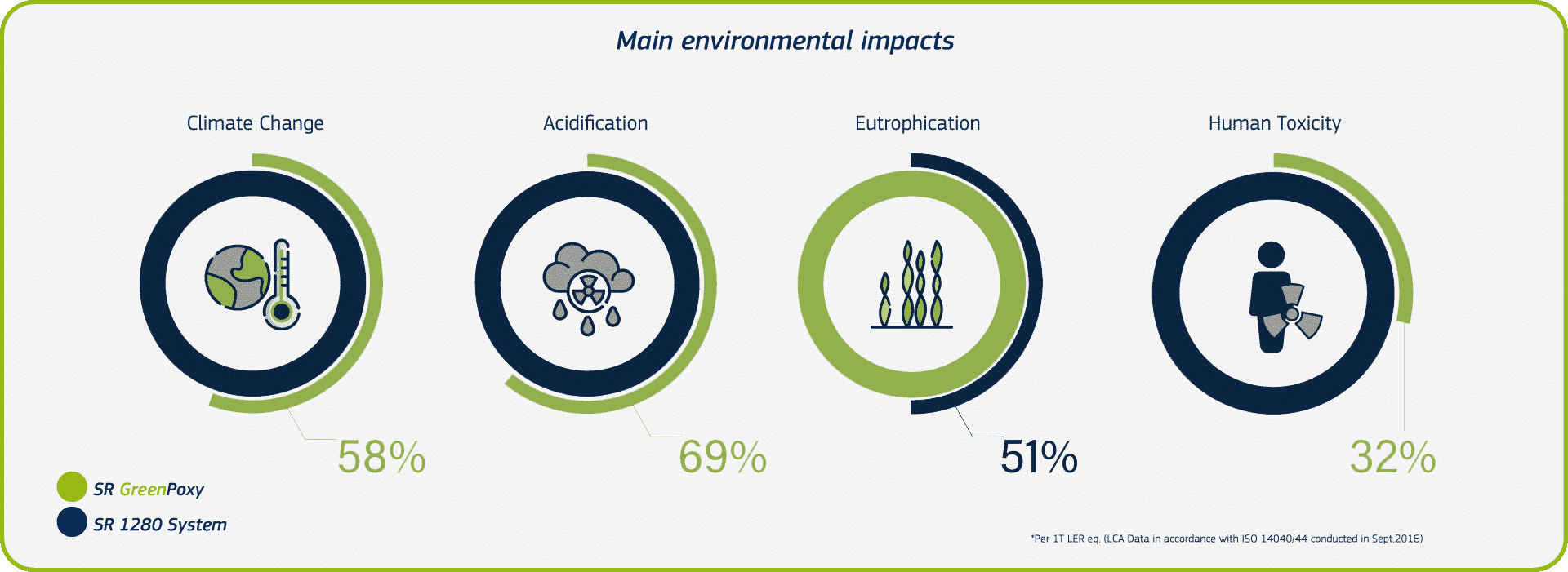
Discussion and conclusion.
The comparison of bio-based and petroleum based LER production, from the point of view of LCA, shows that in almost all applied impact categories the bio based route is more environmentally considerate in comparison to the petroleum route (Tab 3: Main environmental impacts). The main reason is the impact of the upstream manufacturing processes and petroleum extraction and refinery processes.
The acidification impact difference, between the different routes is less important than the other impacts. The main reason is in upstream process: desulfurization of crude petroleum balanced against pesticide production.
Bio-based production of LER is generally less environmentally serious in comparison to petroleum-based production. However, there is are an expected shift in impact on the Eutrophication phenomena. This is because of pesticide and fertilizer application during oil-seed plantation for biodiesel production.
Normative References.
Product Classification Group (PCR): UN CPC 341 – Basic Organic Chemicals.
ISO 14040 (2006). International Standard (ISO): Environmental management – Life cycle assessment: Principles and framework.
ISO 14044 (2006). International Standard (ISO): Environmental management – Life cycle assessment: Requirements and Guidelines.
ISO 14006 (2011). International Standard (ISO): Environmental management – Guidelines for incorporating ecodesign.
ISO 14024 (2016). International Standard (ISO): Environmental labels and declarations – Type I environmental labelling – Principles and procedures
ISO 14021 (2001). International Standard (ISO): Environmental labels and declarations – Self-declared environmental claims (Type II environmental labelling)
ISO 14025 (2010). International Standard (ISO): Environmental labels and declarations – Type III environmental declarations – Principles and procedures