Sicomin is committed to producing chemicals in a more environmentally responsible manner. By using renewable feedstock, eliminating a portion of greenhouse gas emissions and substantially reducing energy consumption, we are practicing greener chemistry that is sustainable.
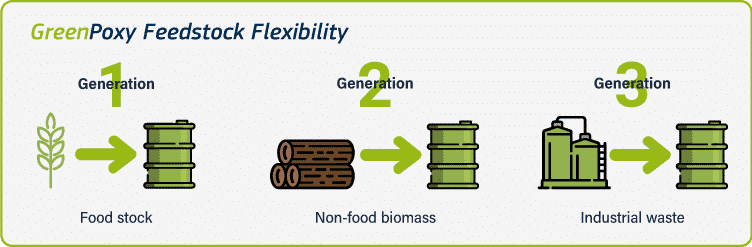
GreenPoxy systems are obtained from 3rd generation bio-based glycerol (oleochemical wastes). Sicomin is focused on using the most abundant bio-based raw material available, but we are also conscious of the need to be as sustainable as possible.


Propylene comes from petroleum extract and refinery industries.
Allylchloride is obtained by direct chlorination of propylene with chlorine in gas phase at rather high temperatures. The stream leaving the reactor is fed to a depropanizer tower which separates overhead hydrogen chloride and propylene from raw allylchloride. The latter is rectified in two column fractionating system. After the washing the resulting wet propylene is compressed, condensed, dried and recycled to the reaction.
Hydrochlorination of glycerin is performed by reacting glycerin with hydrochloric acid. Chlorohydrination of allylchloride is performed by reacting allylchloride with hypochlorous acid. The rectified allylchloride or glycerin, water and chlorine react at nearly ambient temperature to give dichlorohydrins with relatively high yields. The hydrolysis of dichlorohydrins to epichlorohydrin, using milk of lime as saponifying agent, is accomplished in distillation tower where epichlorohydrin is stripped by live steam injected to the bottom of the tower. Wastewater is taken off from the bottom of stripper, while an organic phase, consisting of raw epichlorohydrin, is separated overhead. The raw epichlorohydrin is rectified in a fractionation column system. In the purification system high purity epichlorohydrin is separated from water and low high boiling impurities.